バラつきのないシンプルなモノづくりが価値の連鎖を生み出す 「シン・彦根モデル」(前編)
乗用車用タイヤの生産拠点である(株)ブリヂストン彦根工場。ブリヂストンがデミング賞を受賞した1968年に操業を開始し、「デミング・プラン」起点の「改善力」をベースに「匠の力」を向上させてきた。今ではその「匠の力」にデジタル技術を掛け合わせ、バラつきのないシンプルなモノづくりを磨き上げ、そこから波及したさまざまな取り組みが、想定以上の価値を創出しているというのだ。ただ、そこまでの道のりは決して一筋縄ではいかなかったという――。今回は、今に至るまでの道のりを従業員たちと共に振り返る。
【お話を伺った彦根工場のみなさん】

(株)ブリヂストン 彦根工場 工場長 中村 真人さん
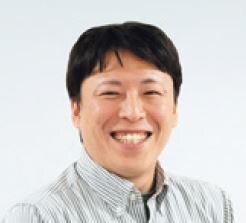
BCMA・G&S推進技術部 技術課 大熊 慎太朗さん
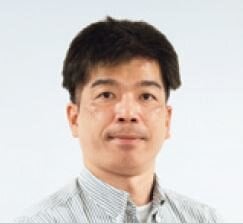
製造部 製造第1課 圧延・才断・ビード係 主任 今村 英明さん
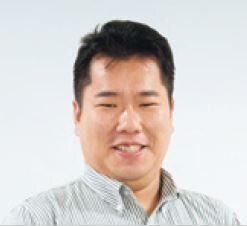
製造部 製造第3課 第3成型係 職長 白橋 優也さん
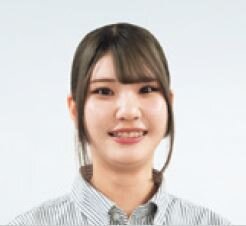
製造部 製造第3課 第3成型係 汐満 純奈さん
モノづくりの本質に向き合い「バラつきのないモノづくり」へチャレンジ
自動成型機「EXAMATION」の導入
「えっ、この機械だけで1直に700本もタイヤを成型できるんですか?」。彦根工場を訪れた見学者は口をそろえて言う。
全自動成型機「EXAMATION(エクサメーション)」の担当である、職長の白橋さんと汐満さんはその実力に胸を張った。この「EXAMATION」を安定稼働させるための工程能力改善こそが今回のテーマとなる「シン・彦根モデル」の原点であった。
遡ること2016年、モノづくりにおいて高品質かつ高い生産性による競争力の向上を目的に、既存成型機の約2倍の生産能力を誇る全自動成型機「EXAMATION」が彦根工場に導入された。
既存成型機では成型者があらかじめ材料工程で準備された部材をドラムに巻き付け、生タイヤといわれる加硫される前のタイヤを成型する。この作業には熟練の技能が必要だ。作業の習得には一定の年月を要し、技能の習熟度の差から新人と熟練者では生産性や成型後の仕上がりにおいて大きな差があった。一方、「EXAMATION」には各所にセンサーが設置されており、400項目を超えるデータを計測・制御しながら全自動で成型するため、高品質なタイヤを均一に生産できる。
しかし、現在の状況に至るまでには相当な苦労があった。その苦労があったことは、この後語られる白橋さんの熱い言葉の一つひとつから容易に想像できた。「EXAMATION」立上げ当時は、安定した生産に課題があったのだ。
当時の開発チームと共に立上げを担当した職長の白橋さんは、400項目に上るデータの解析から、製品不良や設備トラブルが頻発する要因は「材料工程の部材バラつきにあった」と語る。これまでは成型工程の技能員が職人技でカバーしていたものの、「EXAMATION」では許容差を超えるバラつきが生じると、生産を止めてしまうのだ。
白橋さんは、材料工程の主任を務める今村さんに協力を仰いだ。部材のバラつきをデータで示し、今まで以上にバラつきのない部材を成型工程に供給する必要があるという共通認識が芽生えた瞬間だった。さらに、これまでの“自工程の工程能力さえ最適化すればよい”という考えから、次の工程であるお客様の視点に立ち、“工程間で連携した品質確保が重要である”というパラダイムシフトが起きた瞬間でもあった。
全自動成型機「EXAMATION(エクサメーション)」の担当である、職長の白橋さんと汐満さんはその実力に胸を張った。この「EXAMATION」を安定稼働させるための工程能力改善こそが今回のテーマとなる「シン・彦根モデル」の原点であった。
遡ること2016年、モノづくりにおいて高品質かつ高い生産性による競争力の向上を目的に、既存成型機の約2倍の生産能力を誇る全自動成型機「EXAMATION」が彦根工場に導入された。
既存成型機では成型者があらかじめ材料工程で準備された部材をドラムに巻き付け、生タイヤといわれる加硫される前のタイヤを成型する。この作業には熟練の技能が必要だ。作業の習得には一定の年月を要し、技能の習熟度の差から新人と熟練者では生産性や成型後の仕上がりにおいて大きな差があった。一方、「EXAMATION」には各所にセンサーが設置されており、400項目を超えるデータを計測・制御しながら全自動で成型するため、高品質なタイヤを均一に生産できる。
しかし、現在の状況に至るまでには相当な苦労があった。その苦労があったことは、この後語られる白橋さんの熱い言葉の一つひとつから容易に想像できた。「EXAMATION」立上げ当時は、安定した生産に課題があったのだ。
当時の開発チームと共に立上げを担当した職長の白橋さんは、400項目に上るデータの解析から、製品不良や設備トラブルが頻発する要因は「材料工程の部材バラつきにあった」と語る。これまでは成型工程の技能員が職人技でカバーしていたものの、「EXAMATION」では許容差を超えるバラつきが生じると、生産を止めてしまうのだ。
白橋さんは、材料工程の主任を務める今村さんに協力を仰いだ。部材のバラつきをデータで示し、今まで以上にバラつきのない部材を成型工程に供給する必要があるという共通認識が芽生えた瞬間だった。さらに、これまでの“自工程の工程能力さえ最適化すればよい”という考えから、次の工程であるお客様の視点に立ち、“工程間で連携した品質確保が重要である”というパラダイムシフトが起きた瞬間でもあった。
データと向き合い、モノづくりの本質を追求
今村さんと白橋さんは、なぜなぜ分析をベースに、どうすれば部材の工程能力の改善ができるのか、工程をまたがったメンバー間で議論を行った。議論のなかで工程間での連携が生まれ、工程全体で工程能力を改善する活動がスタートした。モノづくりの本質を追求した活動により、バラつきは大幅に改善し、「EXAMATION」の生産性は向上。その能力をいかんなく発揮した。
この活動を起点に、製品の出来栄えや品質に影響する項目をセンサーで連続的に測定し、得られたデータを活用した「見える化」が活発になっていった。こうして、工程全体での本質的な課題を可視化し、工程能力を改善する活動が「彦根モデル」として定着していくこととなる。
この活動を起点に、製品の出来栄えや品質に影響する項目をセンサーで連続的に測定し、得られたデータを活用した「見える化」が活発になっていった。こうして、工程全体での本質的な課題を可視化し、工程能力を改善する活動が「彦根モデル」として定着していくこととなる。
「彦根モデル」として他工場に展開
人によるすり合わせを当たり前としていた既存ラインへの展開拡大
工程全体で工程能力を改善するこうした活動は「彦根モデル」として、「EXAMATION」だけにとどまらず、既存の工程でも取り組まれることに。2021年にはこれまでに得られた知見を他の成型機にも活用していく動きが出てきたのだった。
今村さんは、当時の気づきを次のように話してくれた。
「『EXAMATION』の工程改善で得た知見は他の成型機でも活用できるのではないかと考えたんです。18インチ以上の高インチサイズを成型する既存ラインへ供給する材料工程でも改善活動を行いました。まず、材料工程においても、生産過程のデータを点ではなく連続して取れるようにし、それを成型機のデータと紐づけるシステムを構築したんです。そうすることで、どこでどのように部材の品質が変化しているか確認できるようになりました。これにより、品質不良の発生に対するクイックアクションや慢性的な課題への対策も取れるようになりました。自分たちが製造した部材の特性を把握することで、材料工程の本質的な改善につなげられました」。
さらにこのデジタル技術を用いて、台車に巻き付けて準備する部材は、巻き始めと巻き終わりでシート部材を引っ張る力を調整する必要があることを解明。それを改善する巻き取り制御装置を新たに導入することでバラつきは大幅に削減され、18インチ以上の高インチサイズを成型する既存ラインでも生産性が大きく向上していったのだった。
今村さんは、当時の気づきを次のように話してくれた。
「『EXAMATION』の工程改善で得た知見は他の成型機でも活用できるのではないかと考えたんです。18インチ以上の高インチサイズを成型する既存ラインへ供給する材料工程でも改善活動を行いました。まず、材料工程においても、生産過程のデータを点ではなく連続して取れるようにし、それを成型機のデータと紐づけるシステムを構築したんです。そうすることで、どこでどのように部材の品質が変化しているか確認できるようになりました。これにより、品質不良の発生に対するクイックアクションや慢性的な課題への対策も取れるようになりました。自分たちが製造した部材の特性を把握することで、材料工程の本質的な改善につなげられました」。
さらにこのデジタル技術を用いて、台車に巻き付けて準備する部材は、巻き始めと巻き終わりでシート部材を引っ張る力を調整する必要があることを解明。それを改善する巻き取り制御装置を新たに導入することでバラつきは大幅に削減され、18インチ以上の高インチサイズを成型する既存ラインでも生産性が大きく向上していったのだった。
工程間で同じデータを見ることで、本質的な改善につなげる
技術課の担当としてデータ解析に奔走した大熊さんは言う。「従来、生産に関するデータは工程ごとに管理され、技術課の担当者のみがチェックしていました。全体最適を意識したモノづくりの本質を追求した改善活動が『彦根モデル』として定着していたこともあり、品質データをクラウドで一元管理し、工程間をまたがっていつでも誰でも簡単に見られるようにしました。現場で起きている異常とデータを紐づけて、異常の要因を正しく、素早く把握できるようになったんです。これまでは知見や勘を基に改善案を出していました。しかしデータで工程をつないだことで、初めて改善すべき本質的な問題箇所を見つけ出せるようになりました。これは大きな飛躍でしたね」。
データの一元管理の効果はそれだけではなかった。現場の技能員もデータを見ながら改善活動に取り組むようになっていったというのだ。“データでものを言う” 意識が工場全体に広がり、工場全体で改善活動が連動していった。
データの一元管理の効果はそれだけではなかった。現場の技能員もデータを見ながら改善活動に取り組むようになっていったというのだ。“データでものを言う” 意識が工場全体に広がり、工場全体で改善活動が連動していった。
データと向き合い、全体最適を意識することで、本質的な改善につながり、人のスキルに依存しないモノづくりができる。こうした彦根工場のデータを活用したモノづくりの本質を追求する活動、「彦根モデル」は、他の工場にも展開され、ブリヂストンのモノづくりの底上げにつながった。
後編では、「彦根モデル」が定着し、「シン・彦根モデル」に進化するまでの道のりに迫ります。
後編では、「彦根モデル」が定着し、「シン・彦根モデル」に進化するまでの道のりに迫ります。
※「コメントする」を押してもすぐにはコメントは反映されません。
管理者にて確認の上、反映されます。コメント掲載基準については こちら をご覧ください。
尚、投稿者につきましては、管理者でも特定できない仕様になっております。