「スルラク生産」の実現は“保全”から!
SEQCD全てを支える保全の仕事
ブリヂストンは、最高の品質をお客様に提供するために、“良いモノを標準通りに作り、標準通りに流せる”スルラクな生産を目指してモノづくりを進めています。その実現には、設備を常に最適な状態に保つ、設備保全が必須となります。
今回はタイヤ生産における設備保全員の育成を担っている保全研修センター長の丸尾さんと保全員の皆さんにお話を伺いました。
ブリヂストンは、最高の品質をお客様に提供するために、“良いモノを標準通りに作り、標準通りに流せる”スルラクな生産を目指してモノづくりを進めています。その実現には、設備を常に最適な状態に保つ、設備保全が必須となります。
今回はタイヤ生産における設備保全員の育成を担っている保全研修センター長の丸尾さんと保全員の皆さんにお話を伺いました。
保全業務とは? 安定した生産活動の実現に不可欠
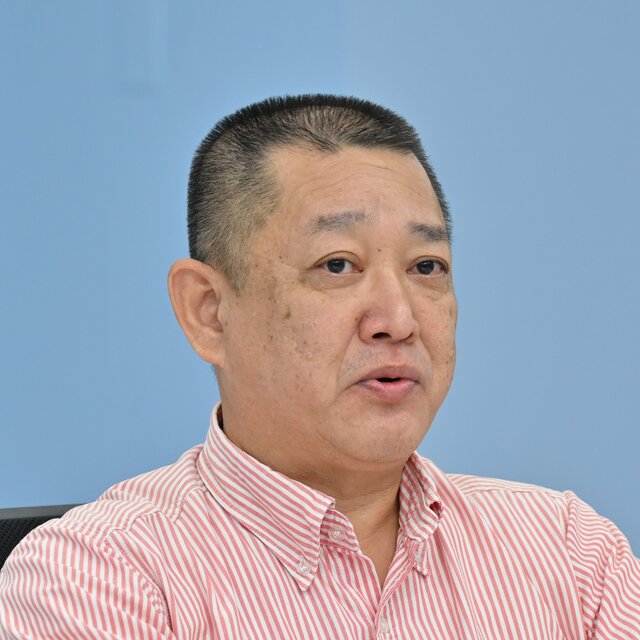
保全研修センター長
丸尾 秀喜さん
Arrow編集部 設備保全の業務について教えてください。
丸尾さん 保全業務とは工場の設備や機械を安全に長く使用できるようにするため、点検や修理を行う仕事です。具体的には、故障が起きた際、原因を究明し復元する「事後保全」、故障を未然に防ぐための「予防保全」、設備が故障した際に今後トラブルが発生しないよう設備そのものを改良する「改良保全」の3つの保全業務があります。これに加え、故障が発生した際に迅速に対応するための予備品管理や、技能のレベル向上のための人財育成にも取り組んでいます。
こうした取り組みがあることで、設備が安全に稼働し、安心・安全な職場環境が実現します。また、安定稼働することで、ロスなく品質の良いものができたり、納期通りにお客様にお届けすることができたりと、保全業務はSEQCD※を支える重要な仕事なんです。
※ 安全・防災(Safety)、環境(Environment)、品質(Quality)、コスト(Cost)、納期(Delivery)
Arrow編集部 保全員の皆さんが工場を支えているんですね。どのようなスキルが必要なんでしょうか?
丸尾さん 保全員に求められるスキルは非常に多いです。例えばタイヤ工場の保全員に必要なスキルは、どの工程にも共通する溶接や仕上げなどの基本技能に加え、精練や成型、加硫、検査といった工程ごとに異なるスキルもあります。タイヤ工場全体としては、5,000以上のスキルが必要になります。
これらのスキルや能力を習得したチームで、生産の要として安定生産に貢献しています。
Arrow編集部 すごい数ですね。これだけ多くのスキルを習得するのは大変そうです。
丸尾さん もちろん一人で5,000以上のスキルを習得する必要があるわけではありません。工場内には、数多くの機械があり、トラブルのパターンもさまざまです。OJTによる担当工程スキルの習得や階層別の教育プログラムを経て、一人ひとりに求められるスキルを習得していくことで、安定稼働を実現しつづける保全チームを形成しています。
また、最近の設備はAI が搭載されるなど、高度化し、デジタルの知識も求められます。一方で、高度化したことで、故障を事前に感知する兆候管理が強化され、トラブル件数が減るという良い面もあります。
丸尾さん 保全業務とは工場の設備や機械を安全に長く使用できるようにするため、点検や修理を行う仕事です。具体的には、故障が起きた際、原因を究明し復元する「事後保全」、故障を未然に防ぐための「予防保全」、設備が故障した際に今後トラブルが発生しないよう設備そのものを改良する「改良保全」の3つの保全業務があります。これに加え、故障が発生した際に迅速に対応するための予備品管理や、技能のレベル向上のための人財育成にも取り組んでいます。
こうした取り組みがあることで、設備が安全に稼働し、安心・安全な職場環境が実現します。また、安定稼働することで、ロスなく品質の良いものができたり、納期通りにお客様にお届けすることができたりと、保全業務はSEQCD※を支える重要な仕事なんです。
※ 安全・防災(Safety)、環境(Environment)、品質(Quality)、コスト(Cost)、納期(Delivery)
Arrow編集部 保全員の皆さんが工場を支えているんですね。どのようなスキルが必要なんでしょうか?
丸尾さん 保全員に求められるスキルは非常に多いです。例えばタイヤ工場の保全員に必要なスキルは、どの工程にも共通する溶接や仕上げなどの基本技能に加え、精練や成型、加硫、検査といった工程ごとに異なるスキルもあります。タイヤ工場全体としては、5,000以上のスキルが必要になります。
これらのスキルや能力を習得したチームで、生産の要として安定生産に貢献しています。
Arrow編集部 すごい数ですね。これだけ多くのスキルを習得するのは大変そうです。
丸尾さん もちろん一人で5,000以上のスキルを習得する必要があるわけではありません。工場内には、数多くの機械があり、トラブルのパターンもさまざまです。OJTによる担当工程スキルの習得や階層別の教育プログラムを経て、一人ひとりに求められるスキルを習得していくことで、安定稼働を実現しつづける保全チームを形成しています。
また、最近の設備はAI が搭載されるなど、高度化し、デジタルの知識も求められます。一方で、高度化したことで、故障を事前に感知する兆候管理が強化され、トラブル件数が減るという良い面もあります。
Arrow編集部 デジタル化の良い面ですね。
丸尾さん ただ、兆候管理が強化されることで、現物現場で感じるトラブルの兆候を見抜く感性を養う機会や技能習得の機会が減り、技能伝承という面では課題もあります。
また、保全員は1工程につき、1〜2人で対応するのが一般的なため、作業が自己流になりがちで、バラつきが生じる可能性があります。そこで、バラつき抑制や保全員の感性を養う機会強化などの課題を解消し、継続的に人財育成を進めていくために、小平にあるグローバル・モノづくり教育センター(G-MEC)での研修やOJTに加えて、2024年7月に保全研修センターを久留米に開所し、育成体制を整えました。
Arrow編集部 保全研修センターが提供できる価値とはどのようなものなのでしょうか?
丸尾さん 保全員として一人前になるためには、①標準を知り、②実践し、③習得して、④技能伝承していくプロセスで育てることが近道ですが、工場では技能伝承の時間が取りづらく、また、必ずしも実践の場数が十分にあるわけではありません。研修センターはそれを補完する役割として、技能や、ブリヂストンの規格に合わせて、業務のPDCAの回し方を学んでもらう場です。また、学んだことを各工場内で広げていただくことで、全体の底上げにつなげたいと思っています。
工場や担当する工程、機械が違っても、実は抱える悩みは共通するところが多くあります。この研修センターで共に学んだメンバー同士、工場間の横のつながりを増やす機会としても活用いただければと考えています。実際、急な設備の補修が必要になった場合などに、予備品を工場間で迅速に融通し合うなどの連携が生まれてきています。
Arrow編集部 今後の展望について教えてください。
丸尾さん 保全は生産活動の基本であるSEQCD全てを支える仕事で、保全員は継続的に知識・技能を高めていく必要があります。今後は高度化する設備や保全難度の高い技能習得の機会を増やすべく、製造機械メーカー様にもご協力いただくなど、研修内容をより充実させていきたいと思います。また、ここでの研修だけでなく、G-MECやOJTを通じた知識や技能の習得の他、他工場のやり方や改善施策を学ぶ機会も設けたいと思います。そして、さまざまな工程を経験したい人、固有の技能を極めたい人など一人ひとりの特性に合わせて、成長のきっかけを提供し続けていきます。
保全研修センターでの技能実習に密着!
今回、保全業務において、あらゆる設備に共通する溶接の実技研修の様子を見せていただきました。
指導員と研修受講者の2人1組で、久留米、甘木、鳥栖の3工場から計6人が参加し、安全を最優先しつつ、溶接の実習に取り組みました。
指導員と研修受講者の2人1組で、久留米、甘木、鳥栖の3工場から計6人が参加し、安全を最優先しつつ、溶接の実習に取り組みました。
指導員
受講者
1 課題制作
まずは研修受講者が溶接を行いました。
まずは研修受講者が溶接を行いました。
指導員による評価
2 破壊試験評価
溶接した完成品を折って、断面に気泡や割れがないか、溶接棒が溶け切っていない部分がないかチェック。不備は強度の低下につながります。実際の作業では、補修したところを破壊してチェックすることはできませんが、自分の作業品質に対して先輩社員からその場でフィードバックをもらえるのは保全研修センターならでは。
2 破壊試験評価
溶接した完成品を折って、断面に気泡や割れがないか、溶接棒が溶け切っていない部分がないかチェック。不備は強度の低下につながります。実際の作業では、補修したところを破壊してチェックすることはできませんが、自分の作業品質に対して先輩社員からその場でフィードバックをもらえるのは保全研修センターならでは。
指導員による評価
3 U曲げ
専用の機械で2〜3トンの圧をかけ、溶接部をUの字に曲げていきます。溶接がうまくいかないと、U字に曲がらず割れてしまいます。
3 U曲げ
専用の機械で2〜3トンの圧をかけ、溶接部をUの字に曲げていきます。溶接がうまくいかないと、U字に曲がらず割れてしまいます。
指導員による評価
4 採点
年に1度グローバルで行われる、グローバル設備保全技能競技会と同じ形式で点数をつけて評価。仲間同士で、互いの点数を見合うことでモチベーションアップ!
4 採点
年に1度グローバルで行われる、グローバル設備保全技能競技会と同じ形式で点数をつけて評価。仲間同士で、互いの点数を見合うことでモチベーションアップ!
参加者コメント
今回研修を受講された皆さんに、研修に参加された感想を聞いてみました。
Arrow編集部 皆さん、研修お疲れ様でした。改めて普段どのような仕事をされているか教えてください。
山﨑さん 私は久留米工場でビード工程の保全を担当しています。保全員は、夜勤時には普段対応することがない機械でも、しっかり対応しなければなりません。また、ただ直すだけでなく、なぜ壊れたのかをしっかりと解析し、直す必要があります。故障の真の原因にたどり着くためには、固定概念にとらわれない柔軟な思考が大切です。
相良さん 久留米工場のマテハンという、成型から検査にタイヤを送る工程の設備を担当しています。学生の頃から、機械や電気のことは学んでいたのですが、工場特有の機械もあり、難しいですね。日々、先輩の知識や技術を見習いつつ、私にも後輩がいるのですが、伝え方が難しく、技能伝承の難しさを実感しています。
武藤さん 私は、甘木工場で検査以外の後工程を担当しています。昔は夜勤で一直に20回ほど呼び出しがかかったこともありますが、先輩方の努力のおかげで、故障件数は減少傾向にあります。しかし、新しい機械や技術の導入によって、故障する箇所や故障の仕方が変わり、求められる技能も変わってきていると感じます。
白水さん 武藤さんと同じく甘木工場なのですが、私は精練工程を担当しています。精練工程は粉体(ダスティングなど)の取り扱いが多いため、まずは修理に取り掛かる前に、掃除から始まります。清掃に2時間程かかることもあるのですが、安全に作業するためにも、故障の原因を突き止めるにも大事な作業です。
三浦さん 私は鳥栖工場の加硫工程を担当しています。加硫工程の機械は、全部で100台以上あるのですが、少人数で対応しているため、いかに故障を未然に防げるかが重要です。故障した際には設備そのものを改良し、同様のトラブルが発生しないように管理しています。
下村さん 三浦さんと同じ鳥栖工場で、部材を運ぶ台車の修理を担当しています。工場全体で数千台の台車があり、突発の故障も多いのですが、月に十数台修理しています。修理は、長いと1台、1時間以上かかることもあります。
Arrow編集部 皆さん、研修お疲れ様でした。改めて普段どのような仕事をされているか教えてください。
山﨑さん 私は久留米工場でビード工程の保全を担当しています。保全員は、夜勤時には普段対応することがない機械でも、しっかり対応しなければなりません。また、ただ直すだけでなく、なぜ壊れたのかをしっかりと解析し、直す必要があります。故障の真の原因にたどり着くためには、固定概念にとらわれない柔軟な思考が大切です。
相良さん 久留米工場のマテハンという、成型から検査にタイヤを送る工程の設備を担当しています。学生の頃から、機械や電気のことは学んでいたのですが、工場特有の機械もあり、難しいですね。日々、先輩の知識や技術を見習いつつ、私にも後輩がいるのですが、伝え方が難しく、技能伝承の難しさを実感しています。
武藤さん 私は、甘木工場で検査以外の後工程を担当しています。昔は夜勤で一直に20回ほど呼び出しがかかったこともありますが、先輩方の努力のおかげで、故障件数は減少傾向にあります。しかし、新しい機械や技術の導入によって、故障する箇所や故障の仕方が変わり、求められる技能も変わってきていると感じます。
白水さん 武藤さんと同じく甘木工場なのですが、私は精練工程を担当しています。精練工程は粉体(ダスティングなど)の取り扱いが多いため、まずは修理に取り掛かる前に、掃除から始まります。清掃に2時間程かかることもあるのですが、安全に作業するためにも、故障の原因を突き止めるにも大事な作業です。
三浦さん 私は鳥栖工場の加硫工程を担当しています。加硫工程の機械は、全部で100台以上あるのですが、少人数で対応しているため、いかに故障を未然に防げるかが重要です。故障した際には設備そのものを改良し、同様のトラブルが発生しないように管理しています。
下村さん 三浦さんと同じ鳥栖工場で、部材を運ぶ台車の修理を担当しています。工場全体で数千台の台車があり、突発の故障も多いのですが、月に十数台修理しています。修理は、長いと1台、1時間以上かかることもあります。
Arrow編集部 今回の研修、いかがでしたか?
相良さん 研修は、溶接に集中できる環境があり、また作業しているところもしっかりと先輩に見てもらえ、その場でフィードバックをもらえるのがありがたかったです。工場で仕事の合間に練習する機会もあるのですが、指導員の方は別の業務をされているので、なかなかしっかりと見てもらうこともアドバイスを頂く機会もありません。ここだと、マンツーマンで見てもらえるのがいいですね。
三浦さん たしかに研修中は工程から呼び出しがかかることもなく、後輩の育成に集中でき、実力もしっかりと把握できますね。その場でフィードバックもできるので、先輩としてもありがたい時間でした。保全員にとって、タイヤ生産に影響を出さないことが何よりも重要です。修理にとどまらず、設備故障の予防を意識して「事後保全」を減らすことを意識して対応しています。
白水さん 普段関わらない他の工場の先輩からも意見を頂けてよかったです。普段は、他の工場の方からフィードバックを頂ける機会はあまりありませんから。また、1年に1度、グローバル設備保全技能競技会があるのですが、他工場の人と横のつながりができたことで、負けたくないという気持ちがさらに強くなりましたね。
下村さん 台車の補修は溶接で直すので、今日の溶接研修は、仕事に直結し、ありがたいです。また、他工場の人たちと一緒に実習することで、自分のレベルを実感し、いい刺激にもなりました。うまい人の技術を見て、あの技術をまねしてみようと参考にもなりました。
武藤さん 工場でさまざまな工程・機械に関する経験を積んでいくのとあわせて、研修センターで基礎的な知識を習得し、技能を磨き上げてもらいたいですね。そして、多くの保全員が真の故障原因を見抜く力を身に付けていければと思います。
山﨑さん 今回この研修センターができたことで、工場間同士のつながりができました。“あそこの工場ではこうやって保全していたよ”と情報が広まると、効率化や標準化も進むと思います。研修センターにはそういったコミュニケーション促進の場としても期待しています。
相良さん 研修は、溶接に集中できる環境があり、また作業しているところもしっかりと先輩に見てもらえ、その場でフィードバックをもらえるのがありがたかったです。工場で仕事の合間に練習する機会もあるのですが、指導員の方は別の業務をされているので、なかなかしっかりと見てもらうこともアドバイスを頂く機会もありません。ここだと、マンツーマンで見てもらえるのがいいですね。
三浦さん たしかに研修中は工程から呼び出しがかかることもなく、後輩の育成に集中でき、実力もしっかりと把握できますね。その場でフィードバックもできるので、先輩としてもありがたい時間でした。保全員にとって、タイヤ生産に影響を出さないことが何よりも重要です。修理にとどまらず、設備故障の予防を意識して「事後保全」を減らすことを意識して対応しています。
白水さん 普段関わらない他の工場の先輩からも意見を頂けてよかったです。普段は、他の工場の方からフィードバックを頂ける機会はあまりありませんから。また、1年に1度、グローバル設備保全技能競技会があるのですが、他工場の人と横のつながりができたことで、負けたくないという気持ちがさらに強くなりましたね。
下村さん 台車の補修は溶接で直すので、今日の溶接研修は、仕事に直結し、ありがたいです。また、他工場の人たちと一緒に実習することで、自分のレベルを実感し、いい刺激にもなりました。うまい人の技術を見て、あの技術をまねしてみようと参考にもなりました。
武藤さん 工場でさまざまな工程・機械に関する経験を積んでいくのとあわせて、研修センターで基礎的な知識を習得し、技能を磨き上げてもらいたいですね。そして、多くの保全員が真の故障原因を見抜く力を身に付けていければと思います。
山﨑さん 今回この研修センターができたことで、工場間同士のつながりができました。“あそこの工場ではこうやって保全していたよ”と情報が広まると、効率化や標準化も進むと思います。研修センターにはそういったコミュニケーション促進の場としても期待しています。
普段は違う工場で働いている参加者同士、実習を通じてさまざまな思いを共有することで、感性を磨き、工場間の横のつながりを増やす機会にもなったようです。
今回は溶接の技能実習に密着しましたが、この他にもBSJPタイヤ生産では、保全業務のPDCAを回すための研修なども行われており、人財育成を強化しています。
※「コメントする」を押してもすぐにはコメントは反映されません。
管理者にて確認の上、反映されます。コメント掲載基準については こちら をご覧ください。
尚、投稿者につきましては、管理者でも特定できない仕様になっております。