ブリヂストンだから、助けられる命がある。災害時に消防隊員の想いに 寄り添うタイヤができるまで。【前編】
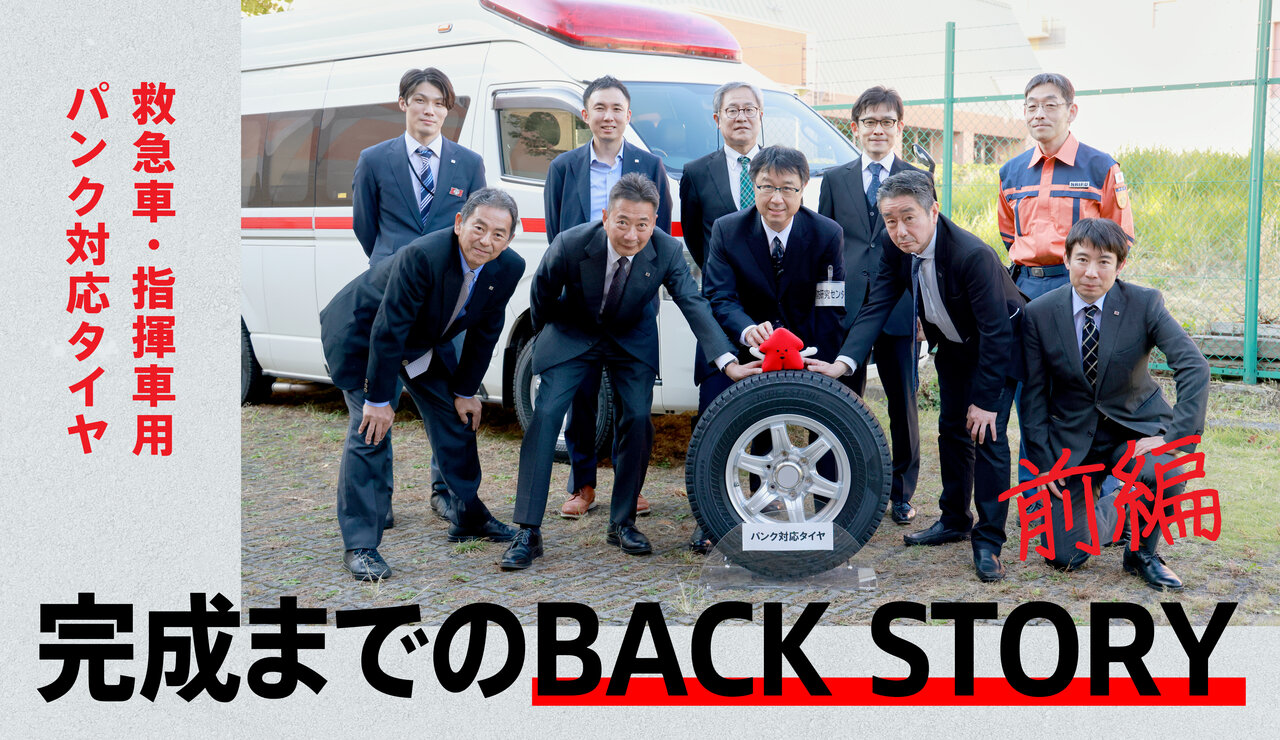
一分一秒でも早く完成させるんだ!
2022年10月、ブリヂストンと総務省消防庁管轄の消防大学校消防研究センターは、世界で初めてとなるタイヤを発表しました。それは、パンクして空気が抜けても走行を続けられる救急車・指揮車用の“パンク対応タイヤ”。今では日本各地の救急車両の足元を支え、人々の命を救うために走り回っています。
携わったメンバーは100人以上。より良いタイヤづくり、そして人命救助への使命感と向き合った4年にわたる日々を、それぞれの視点から追いました。
2022年10月、ブリヂストンと総務省消防庁管轄の消防大学校消防研究センターは、世界で初めてとなるタイヤを発表しました。それは、パンクして空気が抜けても走行を続けられる救急車・指揮車用の“パンク対応タイヤ”。今では日本各地の救急車両の足元を支え、人々の命を救うために走り回っています。
携わったメンバーは100人以上。より良いタイヤづくり、そして人命救助への使命感と向き合った4年にわたる日々を、それぞれの視点から追いました。
※所属部署は取材当時のもの
どんな悪路も乗り越えて患者の元へ駆けつけたい
昨今、日本各地で頻発している自然災害。厳しい状況のなかでも、人命救助という使命を持って現場の最前線へと進んでいくのが、救急車や指揮車※だ。しかし2016年4月、最大震度7を記録した熊本地震では、散乱した瓦礫や道路の亀裂によって救急車のタイヤがパンクすることが懸念され、迂回を余儀なくされるなど患者の救護や搬送に大きな影響が発生した。
悪路でも走り続けられるタイヤがあったなら――。熊本地震で悔しい思いをした救急隊員たちの想いは、全国消防長会から総務省へ要望書として届けられた。これを受け、2018年に消防研究センターは「救急車・指揮車用パンク対応タイヤ共創プロジェクト」の立ち上げを決定。日本自動車タイヤ協会(JATMA)に声をかけた。数多くの企業がパンクしても走行し続けられるタイヤの研究を続けているが、患者を運ぶための乗り心地と耐久性の両立は非常に難題で、小型トラック・バス用タイヤ(LTタイヤ)サイズでは実現できていない現状があった。共同研究に手を挙げたのはブリヂストン、ただ1社だった。
「日々、体を張って危険な場所へ救助に行っている救急隊の方々は、パンク対応タイヤに並々ならぬ想いを持っていました。話しぶりや真っすぐな目に、人命救助に懸ける使命感が溢れていましたね」。プロジェクトの舵取りを任された吉野さんは、消防研究センターの方々と初めて顔を合わせた日のことをそう振り返る。「長い歴史の中でさまざまな価値を生み出してきたブリヂストンなら、まだ世の中にないタイヤを作り上げられるという自信がありました」。
いつ何時発生するかわからない甚大災害に対し、プロジェクトを悠長に進める暇はない。共同研究期間はタイヤ開発には短すぎる3年間。すぐさま関連する社内7部署からメンバーが集められた。超短期間で高性能なタイヤを開発することへの不安感からか、社内キックオフでは「タイヤのプロとして中途半端なものを出したくない」「実現するまでに時間が足りないのでは」という意見が飛び交った。そんななか、吉野さんが口を開いた。
「このタイヤで救える命があるんだ!」。
会議室に響いたこの言葉に、メンバーたちは心を奪われた。救急隊員の真剣な思いに応えたい。つくれないタイヤがあるならば、やるしかない。私たちにしかできないことをやってみせよう。メンバーの決意が固まった瞬間だった。
※指揮車 各種の災害現場において指揮拠点として運用することを目的とした車両
悪路でも走り続けられるタイヤがあったなら――。熊本地震で悔しい思いをした救急隊員たちの想いは、全国消防長会から総務省へ要望書として届けられた。これを受け、2018年に消防研究センターは「救急車・指揮車用パンク対応タイヤ共創プロジェクト」の立ち上げを決定。日本自動車タイヤ協会(JATMA)に声をかけた。数多くの企業がパンクしても走行し続けられるタイヤの研究を続けているが、患者を運ぶための乗り心地と耐久性の両立は非常に難題で、小型トラック・バス用タイヤ(LTタイヤ)サイズでは実現できていない現状があった。共同研究に手を挙げたのはブリヂストン、ただ1社だった。
「日々、体を張って危険な場所へ救助に行っている救急隊の方々は、パンク対応タイヤに並々ならぬ想いを持っていました。話しぶりや真っすぐな目に、人命救助に懸ける使命感が溢れていましたね」。プロジェクトの舵取りを任された吉野さんは、消防研究センターの方々と初めて顔を合わせた日のことをそう振り返る。「長い歴史の中でさまざまな価値を生み出してきたブリヂストンなら、まだ世の中にないタイヤを作り上げられるという自信がありました」。
いつ何時発生するかわからない甚大災害に対し、プロジェクトを悠長に進める暇はない。共同研究期間はタイヤ開発には短すぎる3年間。すぐさま関連する社内7部署からメンバーが集められた。超短期間で高性能なタイヤを開発することへの不安感からか、社内キックオフでは「タイヤのプロとして中途半端なものを出したくない」「実現するまでに時間が足りないのでは」という意見が飛び交った。そんななか、吉野さんが口を開いた。
「このタイヤで救える命があるんだ!」。
会議室に響いたこの言葉に、メンバーたちは心を奪われた。救急隊員の真剣な思いに応えたい。つくれないタイヤがあるならば、やるしかない。私たちにしかできないことをやってみせよう。メンバーの決意が固まった瞬間だった。
※指揮車 各種の災害現場において指揮拠点として運用することを目的とした車両
※所属部署は取材当時のもの
タイヤのプロとして現場のニーズにとことん寄り添う
消防研究センターが求めるタイヤとは、具体的にどのような性能のものなのか。開発の仕事は、ヒアリングと要件定義の取りまとめから始まった。「カウンターパートの消防研究センター 特殊災害研究室の久保田室長は当初、甚大災害が発生したときにのみ、パンク対応タイヤに履き替えて運用することを想定していました。それではこのタイヤが平時に消防署の倉庫で埃を被ってしまうだけでなく、現場の救急隊員の方々からの「日々の救急搬送時でもぜひ使用したい」という声に応えることができない。そこで、雪が降ったときでも履き替えの必要のないスタッドレスタイヤでの開発をご提案したんです。また、パンクした状態で何㎞走行できる性能を目指すのか、出動状況などから導き出すことにしました」(吉野さん)。
タイヤのプロとして要件定義を整理する一方、3年間という期限の中でパンク対応タイヤを完成させるには開発要件が完全に決まるまで待っていられない現状があった。開発チームの1人、野本さんは「通常であれば緻密な要件定義・試算のもと、試作品を作ります。今回は大枠のヒアリング内容をもとに試作品を数多く作り、テストしながら要件を固めていくという、これまでにない開発手順で進めていきました」と語る。“物理的最速”で試作品を作り上げるべく、研究に取り掛かった。
タイヤのプロとして要件定義を整理する一方、3年間という期限の中でパンク対応タイヤを完成させるには開発要件が完全に決まるまで待っていられない現状があった。開発チームの1人、野本さんは「通常であれば緻密な要件定義・試算のもと、試作品を作ります。今回は大枠のヒアリング内容をもとに試作品を数多く作り、テストしながら要件を固めていくという、これまでにない開発手順で進めていきました」と語る。“物理的最速”で試作品を作り上げるべく、研究に取り掛かった。
「形状を保てない!」LTタイヤサイズの壁
実はブリヂストンは過去に一度、救急車用パンク対応タイヤの開発に挑戦したことがあった。自動車メーカーの依頼で2013年に取り組んだ際は、パンクしても走行し続けられる夏用タイヤを実現するべく、試作品のテスト段階まで進んでいた。「データやノウハウが生かせるはずですから、“5年前の延長戦”だという心持ちで開発に着手しました」(野本さん)。過去の蓄積が役立つかもしれない、そんな淡い期待も束の間、メンバーの前には数多くの難題が立ちはだかった。
夏用タイヤとスタッドレスタイヤで、まずトレッド部分を開発し直す必要があったが、それよりも大きな障害となったのは、タイヤのサイズだった。今回のパンク対応タイヤの開発の基盤となるのは、サイド部分の補強などによって空気圧がゼロになった状態でも所定のスピードで一定距離の走行を可能とする技術「ランフラットテクノロジー」。しかし、乗用車用タイヤ(PSタイヤ)以上のサイズでの利用は想定していなかった。なぜならLTサイズのタイヤは重い車両重量を支えるため必要な空気量が多く内圧が高く、パンク後も形状を保ち続けることが困難だからだ。また、パンク後のタイヤは内部が高温となる。これも形状を保つことを阻む要因となっていた。
開発チームはまずサイド補強材の改善に取り組んだ。「サイド補強材として硬い素材を採用したことで、タイヤを加硫するときの金型(モールド)と生タイヤの密着度が下がってしまいました。50本加硫しても数本しか良品が得られず、心が折れそうになった時もありましたね」(野本さん)。補強材の厚みの調整に尽力した渡辺さんは、「単にサイド補強ゴムを分厚く、硬くすれば良いということではありません。なぜなら負荷が別の箇所に集中し、耐久性が損なわれる可能性があったからです。現に、乗用車用タイヤには見られないような壊れ方をした試作品もありました」という。
開発工場の技能員と協力しながら、厚みの異なるサイド部材を20種類以上試作。更に、加硫時のタイヤを金型に押し付ける圧力にも調整を重ね、熱に強く、しっかりとタイヤの荷重を支えられるサイド構造を作り上げた。
夏用タイヤとスタッドレスタイヤで、まずトレッド部分を開発し直す必要があったが、それよりも大きな障害となったのは、タイヤのサイズだった。今回のパンク対応タイヤの開発の基盤となるのは、サイド部分の補強などによって空気圧がゼロになった状態でも所定のスピードで一定距離の走行を可能とする技術「ランフラットテクノロジー」。しかし、乗用車用タイヤ(PSタイヤ)以上のサイズでの利用は想定していなかった。なぜならLTサイズのタイヤは重い車両重量を支えるため必要な空気量が多く内圧が高く、パンク後も形状を保ち続けることが困難だからだ。また、パンク後のタイヤは内部が高温となる。これも形状を保つことを阻む要因となっていた。
開発チームはまずサイド補強材の改善に取り組んだ。「サイド補強材として硬い素材を採用したことで、タイヤを加硫するときの金型(モールド)と生タイヤの密着度が下がってしまいました。50本加硫しても数本しか良品が得られず、心が折れそうになった時もありましたね」(野本さん)。補強材の厚みの調整に尽力した渡辺さんは、「単にサイド補強ゴムを分厚く、硬くすれば良いということではありません。なぜなら負荷が別の箇所に集中し、耐久性が損なわれる可能性があったからです。現に、乗用車用タイヤには見られないような壊れ方をした試作品もありました」という。
開発工場の技能員と協力しながら、厚みの異なるサイド部材を20種類以上試作。更に、加硫時のタイヤを金型に押し付ける圧力にも調整を重ね、熱に強く、しっかりとタイヤの荷重を支えられるサイド構造を作り上げた。
また、パンク時にタイヤの変形が大きくなり内部が高温になって故障する対策として、サイド部の外側に空気の乱気流を起こすことでタイヤを冷却するクーリングフィン機能をつけた。このようなトライ&エラーを重ね、パンクをしても一定の速度と距離で走行できるタイヤの大枠が、目標通り物理的最速で固められていった。
耐久性を突き詰めた結果、リムとの相性が……二律背反の両立を叶える
サイド補強ゴムや素材など、耐久性の高いタイヤを極めていった結果、タイヤはどんどん硬さを増していった。その結果、タイヤがホイールにうまくフィットしなかったり、走行中にタイヤがホイールから外れてしまうリム外れが発生したりと、硬さを起因とした問題が発生した。
耐久性とリム外れ防止を両立させたのが山下さんだ。「試作品はホイールにタイヤを組むための専用機械『チェンジャー』を破壊してしまったほどの強度を持っていました。履けないタイヤ、走行中に外れる可能性があるタイヤを作っても意味がありません。何度も微調整を重ね、パンクして空気が抜けても走行可能な耐久性を維持しながら、リムにフィットするビード部分の厚みや形状を調整しました」。
試作したタイヤは数知れず。開発工場の技能員の協力もあり、2018年の冬に初めての試乗へと漕ぎ着けた。
耐久性とリム外れ防止を両立させたのが山下さんだ。「試作品はホイールにタイヤを組むための専用機械『チェンジャー』を破壊してしまったほどの強度を持っていました。履けないタイヤ、走行中に外れる可能性があるタイヤを作っても意味がありません。何度も微調整を重ね、パンクして空気が抜けても走行可能な耐久性を維持しながら、リムにフィットするビード部分の厚みや形状を調整しました」。
試作したタイヤは数知れず。開発工場の技能員の協力もあり、2018年の冬に初めての試乗へと漕ぎ着けた。
タイヤへの負荷を再現
試作品のテストが行われたのは、栃木県にある「ブリヂストンプルービンググラウンド(BSPG)」。現役を退いた救急車を特別に消防研究センターから借り受けた。実車評価を担った小澤さんと天満屋さんは「運転してみてわかったのですが、他の車と救急車はタイヤにかかる負荷がまるで違ったんです」と語る。救急車は大量の医療機器を積む上、救急隊員や患者、そのご家族も乗車するため、タイヤにかかる荷重が高い。車両前方の屋根部分にパトランプがついているため、一般的な車両よりも重心が上にあることもわかった。また、「消防研究センターの方から運転状況をお聞きしたところ、法定速度内でできるだけ早く現場に到着するため、急ブレーキや急なハンドル操作といったタイヤに負担がかかる走行方法が常態化していることがわかりました」(小澤さん)。
この発見をもとに、テスト時はできるだけ実際の使用状況に近い状態を再現することとなった。医療機器の重量と最大8人が乗車することを想定し、天満屋さんはテストのたびに車両へ約480㎏の重りを運び込んだ。更に、実際の使用条件よりも厳しい条件でも“リム外れ”が起きないことを確認し、意図的に急なハンドリングをして車体を揺さぶったり、パンクさせた状態で走行したりと、強い負荷をかけながらテストを実施。このような厳しい試験を通じて安全を担保した。
「もし車が横転したら、運転する僕らも命の危機にさらされます。安全に最大限配慮しながら使用状況を把握したうえで、実際に使用される以上の厳しい状況を再現し、テストすること。誰かの命のために、勇気を持って取り組みました」(天満屋さん)。数十種類の試作品を丁寧にテストし、開発チームへフィードバック。何度も、実車実験が繰り返された。
この発見をもとに、テスト時はできるだけ実際の使用状況に近い状態を再現することとなった。医療機器の重量と最大8人が乗車することを想定し、天満屋さんはテストのたびに車両へ約480㎏の重りを運び込んだ。更に、実際の使用条件よりも厳しい条件でも“リム外れ”が起きないことを確認し、意図的に急なハンドリングをして車体を揺さぶったり、パンクさせた状態で走行したりと、強い負荷をかけながらテストを実施。このような厳しい試験を通じて安全を担保した。
「もし車が横転したら、運転する僕らも命の危機にさらされます。安全に最大限配慮しながら使用状況を把握したうえで、実際に使用される以上の厳しい状況を再現し、テストすること。誰かの命のために、勇気を持って取り組みました」(天満屋さん)。数十種類の試作品を丁寧にテストし、開発チームへフィードバック。何度も、実車実験が繰り返された。
さまざまな環境で 安全な走行を立証
BSPGでのテストを経て、プロジェクトは実証実験のフェーズへ。消防研究センターの呼びかけや消防署内での評判もあり、国内5カ所の消防本部にご協力いただけることとなった。都市部、山間地、積雪や凍結、台風など、気候や条件の異なる路面でもパンク対応タイヤは性能を発揮。約1年で計42万㎞を走破した。
設計チームや実車評価チームも実証実験に同行。走行距離といったデータ面での検証に加え、ストレッチャーに乗るなどして乗り心地も確認し、設計改善につなげていった。
「実証実験中4カ所でパンクが発生したのですが、走行し続けることができました。改善点ももちろんたくさんあったのですが、消防本部の方から『このタイヤはすごい、人命救助に大きな意味がありますよ』『早く販売してほしいです』といった期待の声をいただけたこと、パンクしても時速40㎞で50㎞程度の走行が可能であることを確認できたことは大きな収穫となりました」(小澤さん)。
「実証実験中4カ所でパンクが発生したのですが、走行し続けることができました。改善点ももちろんたくさんあったのですが、消防本部の方から『このタイヤはすごい、人命救助に大きな意味がありますよ』『早く販売してほしいです』といった期待の声をいただけたこと、パンクしても時速40㎞で50㎞程度の走行が可能であることを確認できたことは大きな収穫となりました」(小澤さん)。
後編へ続きます。
※「コメントする」を押してもすぐにはコメントは反映されません。
管理者にて確認の上、反映されます。コメント掲載基準については こちら をご覧ください。
尚、投稿者につきましては、管理者でも特定できない仕様になっております。