目指すのは”品質トラブルゼロ” 多様な視点からアプローチできる人財へ
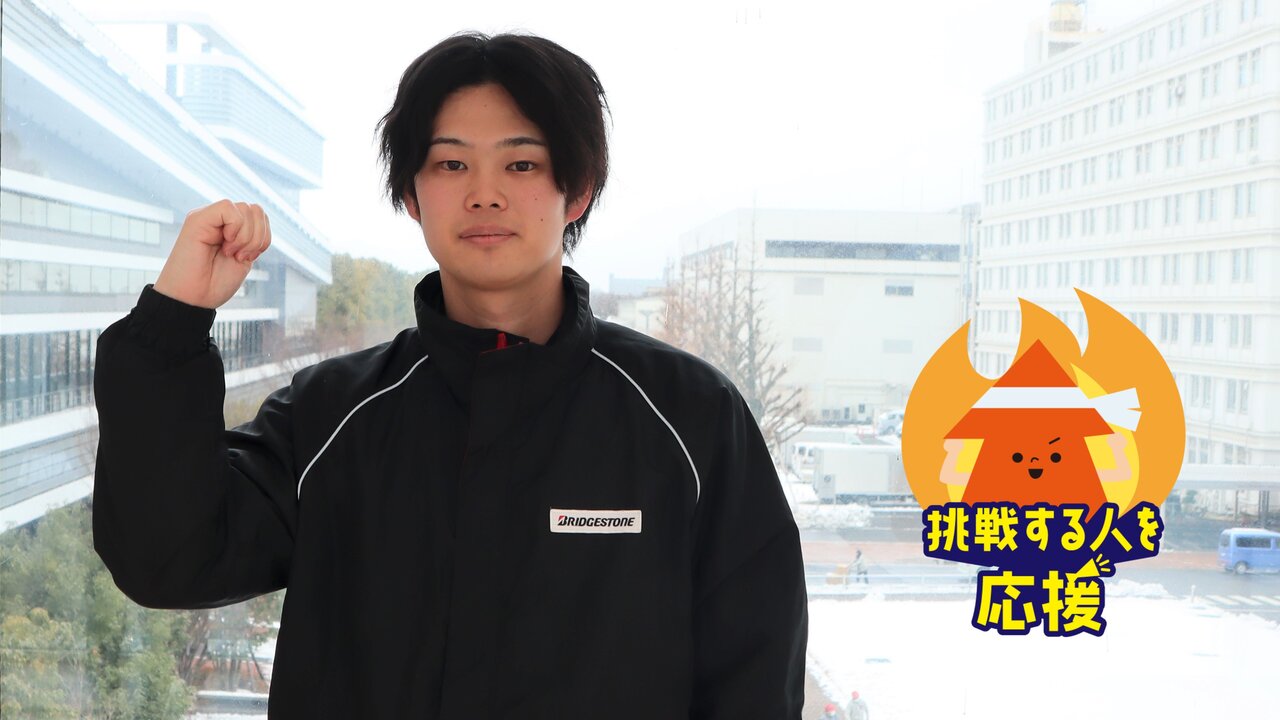
ブリヂストンには創業期から困難なことに「挑戦」し、「品質にこだわり」、「現物現場」で「お客様の困りごとに寄り添う」というDNAが受け継がれ、さまざまな立場や持ち場で日々、挑戦を続ける多くの仲間達がいます。(株)ブリヂストンでは、挑戦意欲のある従業員の皆さんに挑戦の機会を提供したいという思いから、自分で選んだテーマに対して、自ら立てた課題や仮説の調査、検証に現場で100日間取り組める人事制度「現場100日チャレンジプログラム」(以下、現場100日チャレンジ)が昨年の4月から始まりました。今回は、リトレッドタイヤの品質保証体制強化に取り組んだ、CQO・品質部門 G原材料・中材品質システム課の西田さんにお話しを伺いました!
「製造」から「市場」へ 新たな視点を求めて現場100日チャレンジへ
Arrow編集部 西田さんの担当業務について教えていただけますか?
西田さん 現場100日チャレンジに参加する前は、乗用車用タイヤやトラック・バス用タイヤに関わらず、タイヤ製造工程で発生する品質トラブルの再発防止に関する対策を検討していました。GBS(Global Business Support)機能として、各SBUで活用可能なグローバル標準を作り、展開する役割です。品質トラブルの多くはヒューマンエラーが原因です。中間材料の使用違い、プロセスの誤設定、表示に関する治工具の取り付け違いなど、さまざまな工程で起こりうるエラーの削減、品質トラブルの再発防止を図ることが私のミッションです。もちろん、これまでもブリヂストンにおいて、長年に渡って取り組んできたテーマではありますが、ヒューマンエラーを未然防止する為の自動化なども推進し、ユーザーであるお客様にご迷惑をかけないために、完全な”品質トラブルゼロ”を目指して取り組んでいます。
西田さん 現場100日チャレンジに参加する前は、乗用車用タイヤやトラック・バス用タイヤに関わらず、タイヤ製造工程で発生する品質トラブルの再発防止に関する対策を検討していました。GBS(Global Business Support)機能として、各SBUで活用可能なグローバル標準を作り、展開する役割です。品質トラブルの多くはヒューマンエラーが原因です。中間材料の使用違い、プロセスの誤設定、表示に関する治工具の取り付け違いなど、さまざまな工程で起こりうるエラーの削減、品質トラブルの再発防止を図ることが私のミッションです。もちろん、これまでもブリヂストンにおいて、長年に渡って取り組んできたテーマではありますが、ヒューマンエラーを未然防止する為の自動化なども推進し、ユーザーであるお客様にご迷惑をかけないために、完全な”品質トラブルゼロ”を目指して取り組んでいます。
Arrow編集部 工程で起こりうるミスを減らし、品質トラブルをゼロに近づけていく。モノづくりの根幹を支える大事な役割ですが、現場100日チャレンジに手を挙げたきっかけを教えてください。
西田さん 直属の上司から紹介されたことがきっかけですが、正直、最初に話を聞いた際は自分の中でピンときませんでした(笑)。ただ、時間が経つにつれ、少しずつ「チャレンジしたい」という気持ちが芽生えてきました。私はそれまで、どちらかというと「製造」に近い立場で、小平の技術センターや彦根工場で品質保証に関する業務に携わってきましたが、業務経験を積んでいくうえで、商品であるタイヤを使って下さるお客様に近い、「市場」側の視点も養いたいという想いが出てきました。また同時に、会社としても注力しているソリューション領域に携わってみたいという気持ちもあったので、リトレッドタイヤをテーマとしたチャレンジに臨みたいと上司に申し出をしました。
西田さん 直属の上司から紹介されたことがきっかけですが、正直、最初に話を聞いた際は自分の中でピンときませんでした(笑)。ただ、時間が経つにつれ、少しずつ「チャレンジしたい」という気持ちが芽生えてきました。私はそれまで、どちらかというと「製造」に近い立場で、小平の技術センターや彦根工場で品質保証に関する業務に携わってきましたが、業務経験を積んでいくうえで、商品であるタイヤを使って下さるお客様に近い、「市場」側の視点も養いたいという想いが出てきました。また同時に、会社としても注力しているソリューション領域に携わってみたいという気持ちもあったので、リトレッドタイヤをテーマとしたチャレンジに臨みたいと上司に申し出をしました。
日本と米国 それぞれの改善フローの回し方
Arrow編集部 ご自分のこれまでの経験も振り返った上で、新しい視点を養いたいと考えたんですね。現場100日チャレンジのテーマである「リトレッドタイヤの品質保証体制強化」ですが、どのように進めていったのでしょうか?
西田さん リトレッドタイヤの製法は大きく分けて2種類あります。一つは、未加硫の生ゴムを台タイヤに貼り付け、モールドに入れて加硫し、溝をつけるHOT方式。もう一つは、あらかじめ加硫してあるトレッドゴムを貼りつけ、加硫缶で加硫するCOLD方式です。それぞれの地区で保有する標準・仕組みをベースにグローバル展開を見据えた「製造QA要件」を作ることが目指すべきゴールです。まずは情報の集めやすさから、日本で主流のHOT方式によるリトレッドタイヤからどのような不良品が発生しているのか、取り組みに着手しました。具体的にはブリヂストンBRM(株)の加須工場にご協力いただき、実際の不良品の格付け作業や、クレーム品として返却されたものを確認する検討会に参加させていただきました。国内での調査が一段落した後は、今度はCOLD方式が主流である米国を訪問しました。ここでは、リトレッドタイヤの廃品や、技術サービスの人たちが集めてきた市場調査の結果から、次の開発や品質保証につなげる会議に出席し、改善サイクルを勉強させていただきました。
西田さん リトレッドタイヤの製法は大きく分けて2種類あります。一つは、未加硫の生ゴムを台タイヤに貼り付け、モールドに入れて加硫し、溝をつけるHOT方式。もう一つは、あらかじめ加硫してあるトレッドゴムを貼りつけ、加硫缶で加硫するCOLD方式です。それぞれの地区で保有する標準・仕組みをベースにグローバル展開を見据えた「製造QA要件」を作ることが目指すべきゴールです。まずは情報の集めやすさから、日本で主流のHOT方式によるリトレッドタイヤからどのような不良品が発生しているのか、取り組みに着手しました。具体的にはブリヂストンBRM(株)の加須工場にご協力いただき、実際の不良品の格付け作業や、クレーム品として返却されたものを確認する検討会に参加させていただきました。国内での調査が一段落した後は、今度はCOLD方式が主流である米国を訪問しました。ここでは、リトレッドタイヤの廃品や、技術サービスの人たちが集めてきた市場調査の結果から、次の開発や品質保証につなげる会議に出席し、改善サイクルを勉強させていただきました。
Arrow編集部 日本と米国、リトレッドタイヤの主流製法の違いも加味した上で、調査を進めていったわけですね。双方の現場を見て印象に残っていることを教えてください。
西田さん 日本の場合、不良品やクレーム品の確認は、関係者が一堂に集まり、現物を1本1本見て、それぞれの状態を念入りに確認した上で、改善フローを回していくというプロセスでした。一方、市場規模が大きい米国では、各州のField Engineering担当が実地確認したデータやITツールを活用して改善を図っていました。それぞれの強みや機能を活かした改善を進めていることを、実際の現場で見ることが出来たのは私にとって大きな経験になりました。
西田さん 日本の場合、不良品やクレーム品の確認は、関係者が一堂に集まり、現物を1本1本見て、それぞれの状態を念入りに確認した上で、改善フローを回していくというプロセスでした。一方、市場規模が大きい米国では、各州のField Engineering担当が実地確認したデータやITツールを活用して改善を図っていました。それぞれの強みや機能を活かした改善を進めていることを、実際の現場で見ることが出来たのは私にとって大きな経験になりました。
不良度合いの大きさ≠クレームの大きさ 「現物現場」での気づき
Arrow編集部 改善フローの進め方の違いを見ることができたんですね。現場を見たことで、何か気づきはありましたか?
西田さん はい。日本では不良品やクレーム品の現物を見たり触ったりする機会が多かったのですが、私はそれまで、お客様からのクレームの強弱は、不良度合いの大きさが大きく影響すると考えていました。ただ実際には、たとえ比較的軽微な不良であっても、お客様にとっては重要であり、場合によってはブリヂストンに対するお客様からの信頼にも大きく影響します。そういった意味でも、製造側から見る不良の度合いと、お客様が感じる不良の度合いは必ずしも一致しないことを学びました。製造現場に近い目線で仕事をしていると、どうしても不良の大きさや程度を重視してしまいがちですが、お客様や市場側の目線を持つことで、ユーザー一人ひとりのタイヤの使い方もイメージしながら、タイヤと向き合えるようになった気がします。現場を見ることで養うことができた感覚の一つです。
西田さん はい。日本では不良品やクレーム品の現物を見たり触ったりする機会が多かったのですが、私はそれまで、お客様からのクレームの強弱は、不良度合いの大きさが大きく影響すると考えていました。ただ実際には、たとえ比較的軽微な不良であっても、お客様にとっては重要であり、場合によってはブリヂストンに対するお客様からの信頼にも大きく影響します。そういった意味でも、製造側から見る不良の度合いと、お客様が感じる不良の度合いは必ずしも一致しないことを学びました。製造現場に近い目線で仕事をしていると、どうしても不良の大きさや程度を重視してしまいがちですが、お客様や市場側の目線を持つことで、ユーザー一人ひとりのタイヤの使い方もイメージしながら、タイヤと向き合えるようになった気がします。現場を見ることで養うことができた感覚の一つです。
コミュニケーションで作り上げた製造QA要件
Arrow編集部 まさに「現物現場」で「お客様の困りごとに寄り添う」経験を積まれたわけですね。今回のゴールである製造QA要件への落とし込む際の苦労はありましたか?
西田さん はい。日本と米国で調査を終えた後、製造QA要件の作成に向けて作業を開始しましたが、実際にはこれに着手する前に、「製造対策リスト」というものを作る必要がありました。製造対策リストは簡単に言うと、「こういうトラブルにはこういう対策が必要だ」という対策案のリストになります。これを製造現場での規格である製造QA要件に落とし込んでいくわけですが、この要件は理想論で構成されたものでは活用できません。製造現場で現実的に運用できるレベルの対策へ落とし込んでいく必要があります。今回の現場100日チャレンジではこの落とし込み作業が一番大変なプロセスでした。この作業においても、加須工場の皆さんにご協力いただいたのですが、密なコミュニケーションをとらせていただき、最終的には関係者全員で納得のいく製造QA要件をつくることができました。メールやチャットでのやり取りではない「Face to Face」の大切さ、現場に飛び込んでいくオープンマインドの重要性を改めて学ぶことができました。
西田さん はい。日本と米国で調査を終えた後、製造QA要件の作成に向けて作業を開始しましたが、実際にはこれに着手する前に、「製造対策リスト」というものを作る必要がありました。製造対策リストは簡単に言うと、「こういうトラブルにはこういう対策が必要だ」という対策案のリストになります。これを製造現場での規格である製造QA要件に落とし込んでいくわけですが、この要件は理想論で構成されたものでは活用できません。製造現場で現実的に運用できるレベルの対策へ落とし込んでいく必要があります。今回の現場100日チャレンジではこの落とし込み作業が一番大変なプロセスでした。この作業においても、加須工場の皆さんにご協力いただいたのですが、密なコミュニケーションをとらせていただき、最終的には関係者全員で納得のいく製造QA要件をつくることができました。メールやチャットでのやり取りではない「Face to Face」の大切さ、現場に飛び込んでいくオープンマインドの重要性を改めて学ぶことができました。
バリューチェーン全体の視点を持った人財を目指して
Arrow編集部 西田さんにとって大きな収穫となった今回の現場100日チャレンジですが、その後の展開や今後の目標について教えてください。
西田さん 100日チャレンジ期間が終わった後、米国訪問でお世話になったBSAM(Bridgestone Americas, Inc.)の関係者にも再度サポートいただき、製造QA要件を欧米に展開することができました。これからも国内に限らず、グローバルでも人脈を広げて、協働する経験を積んでいきたいです。またチャレンジ前に自分の中でテーマとしていた、「市場」側の視点についても学ぶ機会をいただくことができました。これからは、原材料、開発といった、よりバリューチェーンの上流についても意識し、さまざまな角度から品質課題と向き合い、解決策を立案できる人財になりたいと考えています!
また最後になりましたが、上司をはじめ、チャレンジ期間中に私が担当していた業務をサポートいただいた皆さんに、改めて感謝の気持ちを伝えたいです。ありがとうございました!
Arrow編集部 さまざまな目線から”品質トラブルゼロ”を目指していく壮大なチャレンジ、今後も応援しています!
西田さん 100日チャレンジ期間が終わった後、米国訪問でお世話になったBSAM(Bridgestone Americas, Inc.)の関係者にも再度サポートいただき、製造QA要件を欧米に展開することができました。これからも国内に限らず、グローバルでも人脈を広げて、協働する経験を積んでいきたいです。またチャレンジ前に自分の中でテーマとしていた、「市場」側の視点についても学ぶ機会をいただくことができました。これからは、原材料、開発といった、よりバリューチェーンの上流についても意識し、さまざまな角度から品質課題と向き合い、解決策を立案できる人財になりたいと考えています!
また最後になりましたが、上司をはじめ、チャレンジ期間中に私が担当していた業務をサポートいただいた皆さんに、改めて感謝の気持ちを伝えたいです。ありがとうございました!
Arrow編集部 さまざまな目線から”品質トラブルゼロ”を目指していく壮大なチャレンジ、今後も応援しています!
ブリヂストンは創業時から、事業を通じて社会に貢献するために絶えず挑戦してきました。「挑戦」はまさにブリヂストンのDNAであり、自身はもちろん、誰かの挑戦を周りの仲間が後押しすることで、また新たなチャレンジが生まれます。そうして一人ひとりの成長と会社の成長が両輪となることで、変化に対応できるレジリアントな“エクセレント”ブリヂストンを実現できます。だからこそ、ブリヂストンはさまざまな施策を通じて、一人ひとりの挑戦をサポートしていきます。グループ報Arrowではそれぞれの立場・持ち場で挑戦を続ける仲間を紹介していきます!
【(株)ブリヂストン HRXカルチャーチェンジ・DE&I推進部より】
(株)ブリヂストンでは 2023年4月以降、計15名の開発企画職の皆さんが、海外含むさまざまな現場での100日チャレンジに取り組んでいます。新しいことへのチャレンジ、ハードルが高いと感じる方も多いと思いますが、普段から自分のやりたいこと、いっしょに働く仲間がやりたいと考えていることを職場内で共有し合い、色々な階層で現物現場での挑戦が生まれるようにしていくためにも、普段から、挑戦しようとしている仲間を後押しする気持ちを持つことが大切だと考えています。日々の業務において認識はしているものの、なかなか打破できないと感じている課題をお持ちの方も多くいらっしゃると思います。3月初めより第3回現場100日チャレンジの募集を開始していますので、100日間、現場で集中して仮説の調査や検証を行い、それらを解決させたいという熱い想いをお持ちの方、ぜひ奮ってご応募ください(募集は5/7まで)!また、西田さんも含めた当プログラムの経験者の方に体験談を語って頂くセッションを3/29(金)に本社地区で開催予定ですので、プログラムに関心がある方はこちらもぜひご参加ください(詳しくはこちら)
(株)ブリヂストンでは 2023年4月以降、計15名の開発企画職の皆さんが、海外含むさまざまな現場での100日チャレンジに取り組んでいます。新しいことへのチャレンジ、ハードルが高いと感じる方も多いと思いますが、普段から自分のやりたいこと、いっしょに働く仲間がやりたいと考えていることを職場内で共有し合い、色々な階層で現物現場での挑戦が生まれるようにしていくためにも、普段から、挑戦しようとしている仲間を後押しする気持ちを持つことが大切だと考えています。日々の業務において認識はしているものの、なかなか打破できないと感じている課題をお持ちの方も多くいらっしゃると思います。3月初めより第3回現場100日チャレンジの募集を開始していますので、100日間、現場で集中して仮説の調査や検証を行い、それらを解決させたいという熱い想いをお持ちの方、ぜひ奮ってご応募ください(募集は5/7まで)!また、西田さんも含めた当プログラムの経験者の方に体験談を語って頂くセッションを3/29(金)に本社地区で開催予定ですので、プログラムに関心がある方はこちらもぜひご参加ください(詳しくはこちら)
※「コメントする」を押してもすぐにはコメントは反映されません。
管理者にて確認の上、反映されます。コメント掲載基準については こちら をご覧ください。
尚、投稿者につきましては、管理者でも特定できない仕様になっております。