天然ゴムとタイヤ製造をデジタルでつなげ! データの活用でより良い品質のタイヤを
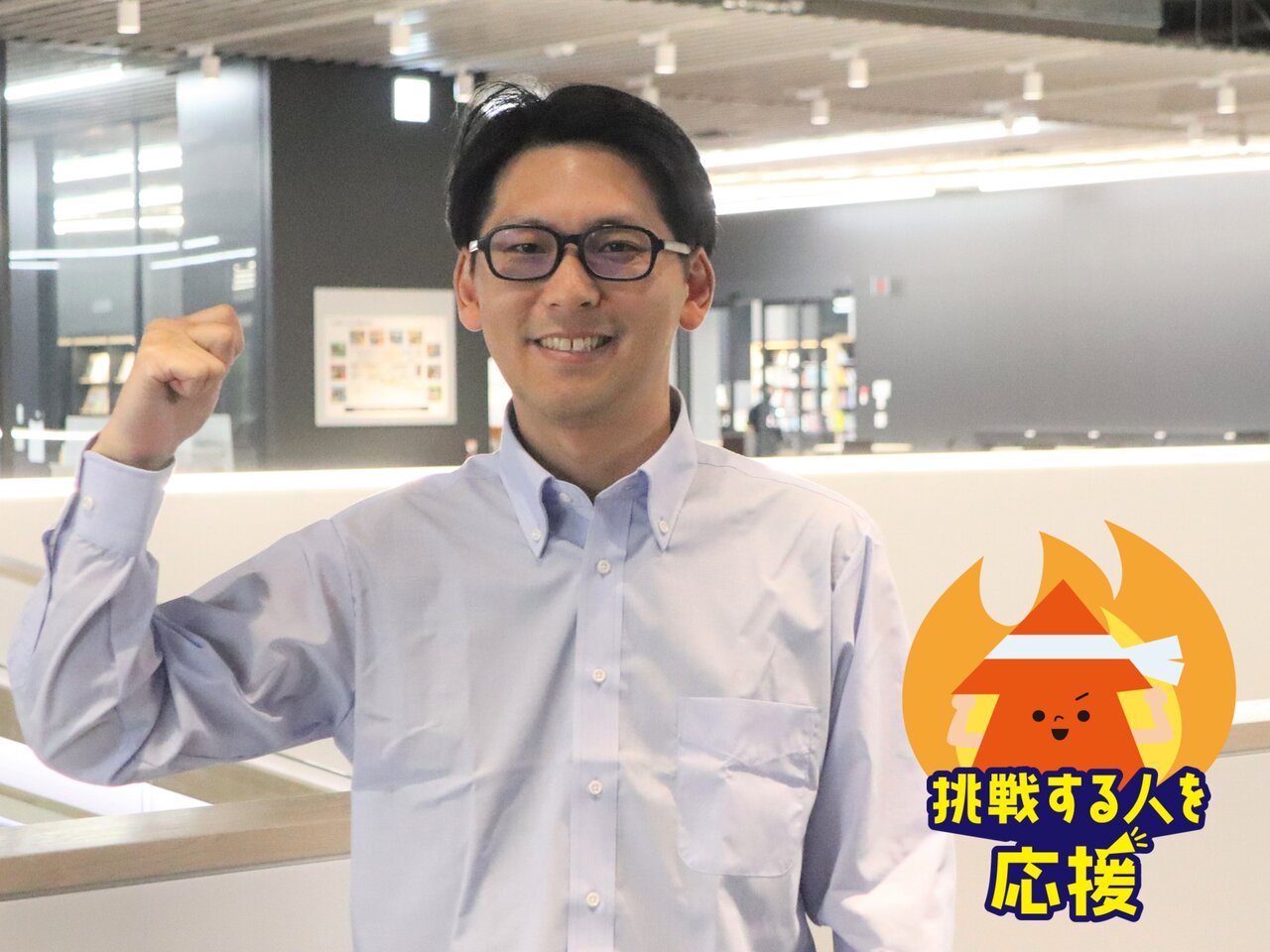
ブリヂストンには創業期から困難なことに「挑戦」し、「品質にこだわり」、「現物現場」で「お客様の困りごとに寄り添う」というDNAが受け継がれ、さまざまな立場や持ち場で日々、挑戦を続ける多くの仲間達がいます。(株)ブリヂストンでは、挑戦意欲のある従業員の皆さんに挑戦の機会を提供したいという思いから、自分で選んだテーマに対して、自ら立てた課題や仮説の調査、検証に現場で100日間取り組める人事制度「現場100日チャレンジプログラム」(以下、現場100日チャレンジ)が2023年の4月から始まりました。今回は、その現場100日チャレンジで奮闘したタイヤ生産基盤改革部門 タイヤ生産システム制御改革課長の出原さんにお話を伺いました!
タイヤモノづくりの長年の課題であるタイヤ部材寸度(長さや幅等)のバラつき改善。その大きな要因が農産物である天然ゴムのバラつきであることから、従来はあきらめていたモノづくりの本質課題でした。この難課題を製造現場だけではなくサプライチェーン全体をデジタルでつなぎ制御することで解決できないか、と考えていた出原さんが、100日間現場で取り組んだ内容を熱く語ってくれました!
タイヤモノづくりの長年の課題であるタイヤ部材寸度(長さや幅等)のバラつき改善。その大きな要因が農産物である天然ゴムのバラつきであることから、従来はあきらめていたモノづくりの本質課題でした。この難課題を製造現場だけではなくサプライチェーン全体をデジタルでつなぎ制御することで解決できないか、と考えていた出原さんが、100日間現場で取り組んだ内容を熱く語ってくれました!
未だに謎の多い天然ゴム ゴム練りによる品質の均一化を目指して
Arrow編集部 現場100日チャレンジが始まる前に、出原さんが担当されていた業務を教えていただけますか?
出原さん 設備の電気制御が担当で、ここ3年くらいはタイヤ製造の精練工程における素練りの粘度安定化に取り組んでいました。天然ゴムなどの原材料は、同じ品種でもロットによってさまざまな細かい物性のバラつきがあります。「天然ゴムは農産物でありバラつくもの。工場ではコントロールできない」という思い込みがあり、これが、私たちが先送りにしてきたタイヤモノづくりの本質課題の一つです。この課題解決にチャレンジし、それらのバラつきをゴム練りの工程でなるべく均一化し、後工程に提供することが、ロスの無いモノづくりへとつながり、プレミアムタイヤ事業へも貢献できると考えています。
出原さん 設備の電気制御が担当で、ここ3年くらいはタイヤ製造の精練工程における素練りの粘度安定化に取り組んでいました。天然ゴムなどの原材料は、同じ品種でもロットによってさまざまな細かい物性のバラつきがあります。「天然ゴムは農産物でありバラつくもの。工場ではコントロールできない」という思い込みがあり、これが、私たちが先送りにしてきたタイヤモノづくりの本質課題の一つです。この課題解決にチャレンジし、それらのバラつきをゴム練りの工程でなるべく均一化し、後工程に提供することが、ロスの無いモノづくりへとつながり、プレミアムタイヤ事業へも貢献できると考えています。
Arrow編集部 タイヤのモノづくりの上流から、ロスを減らす取り組みに注力されていたんですね。今回の現場100日チャレンジに手を挙げたきっかけを教えていただけますか?
出原さん 当時の上司からこういうものがあると紹介され、すぐに「やらせてください!」と手を挙げました。過去、練り途中の実績データを元に、ゴムの粘度を推測する評価方法確立にチャレンジしてきましたが、目標とする練りゴムのバラつき解消には至っていません。これまで同様に、本質課題である農産物の壁にぶち当たり、諦めかけていた時にこの話がありました。現場100日チャレンジを通じ、「いままで見たこともなかった天然ゴムの製造現場をじっくり調査して理解することができれば、タイヤ工場の現場では思いつかなかった、今までにない新しい発想が生まれるかもしれない。」 これは、大きなチャンスだと思いました。
出原さん 当時の上司からこういうものがあると紹介され、すぐに「やらせてください!」と手を挙げました。過去、練り途中の実績データを元に、ゴムの粘度を推測する評価方法確立にチャレンジしてきましたが、目標とする練りゴムのバラつき解消には至っていません。これまで同様に、本質課題である農産物の壁にぶち当たり、諦めかけていた時にこの話がありました。現場100日チャレンジを通じ、「いままで見たこともなかった天然ゴムの製造現場をじっくり調査して理解することができれば、タイヤ工場の現場では思いつかなかった、今までにない新しい発想が生まれるかもしれない。」 これは、大きなチャンスだと思いました。
現物現場で気がついた仮説と実態のギャップ
Arrow編集部 天然ゴムの製造現場を調査対象に絞ったわけですね。現場100日チャレンジではどのような拠点を訪問調査したのでしょうか?
出原さん 天然ゴムの作り方や、そもそもバラつきはどこで生まれるのかなどを調べる上で、まずはインドネシアにあるBridgestone Sumatra Rubber Estate(BSRE)を訪問させて頂き、天然ゴムそのものに関する知識の習熟や、調査ポイントの最終確認を行いました。その後は外部の天然ゴム加工工場を7か所、加えて2拠点の天然ゴム農家を回り、どこで物性のバラつきが発生しているのかを現物現場で調べました。
訪問して初めてわかったことなのですが、BSREと外部の天然ゴム加工工場では一部の製造ラインが異なっていたため、その場で現物を見ながら、状況に応じて質問を考え、ヒアリングする必要がありました。1社への調査時間は1日しかかけられないという時間の制約もあったので、その場での質疑応答でこちらが内容を理解できないと、事後での問い合わせはできません。聞き逃しは許されないという緊張感の中での調査を進めました。また、調査先からホテルに戻ってからも、忘れないうちに調査結果を纏め、現場で新たに聞いたこと、わかったことを質問シートに反映し、次の訪問調査へ活用していきました。
出原さん 天然ゴムの作り方や、そもそもバラつきはどこで生まれるのかなどを調べる上で、まずはインドネシアにあるBridgestone Sumatra Rubber Estate(BSRE)を訪問させて頂き、天然ゴムそのものに関する知識の習熟や、調査ポイントの最終確認を行いました。その後は外部の天然ゴム加工工場を7か所、加えて2拠点の天然ゴム農家を回り、どこで物性のバラつきが発生しているのかを現物現場で調べました。
訪問して初めてわかったことなのですが、BSREと外部の天然ゴム加工工場では一部の製造ラインが異なっていたため、その場で現物を見ながら、状況に応じて質問を考え、ヒアリングする必要がありました。1社への調査時間は1日しかかけられないという時間の制約もあったので、その場での質疑応答でこちらが内容を理解できないと、事後での問い合わせはできません。聞き逃しは許されないという緊張感の中での調査を進めました。また、調査先からホテルに戻ってからも、忘れないうちに調査結果を纏め、現場で新たに聞いたこと、わかったことを質問シートに反映し、次の訪問調査へ活用していきました。
Arrow編集部 各社訪問時の気づきも活かしながら、調査を進めていったんですね。テーマそのものについて、現物現場で得られた学びについて教えてください。
出原さん まず、天然ゴム製造においては、ゴムの木の樹液(ラテックス)をカップに採取するところから始まります。カップに採取したラテックスを固めたものをカップランプといいます。複数農家で生産された多くのカップランプを集め、粉砕~洗浄~混合~乾燥のプロセスを経て、大きな天然ゴムのブロックを作り上げていきます。これが一つのロットになります。現場に行くまでは、この一連のプロセスを経れば、投入された個々のカップランプが良く混ざりあい、同じロット内での品質バラつきはほぼ平準化されると思っていました。ところが、実際は同一ロットの中でも、特定の農家のカップランプの成分が偏るなど、こちらが期待していたほど平準化されていないことがわかったんです。
出原さん まず、天然ゴム製造においては、ゴムの木の樹液(ラテックス)をカップに採取するところから始まります。カップに採取したラテックスを固めたものをカップランプといいます。複数農家で生産された多くのカップランプを集め、粉砕~洗浄~混合~乾燥のプロセスを経て、大きな天然ゴムのブロックを作り上げていきます。これが一つのロットになります。現場に行くまでは、この一連のプロセスを経れば、投入された個々のカップランプが良く混ざりあい、同じロット内での品質バラつきはほぼ平準化されると思っていました。ところが、実際は同一ロットの中でも、特定の農家のカップランプの成分が偏るなど、こちらが期待していたほど平準化されていないことがわかったんです。
Arrow編集部 事前の予測と、現物現場で確認した結果に相違があったということですね。
出原さん その通りです。現場100日チャレンジに限らず、仕事を進める上では自分なりの仮説を立てて、アプローチをしていくことはとても大切だと思うのですが、それが先入観のように、強い思い込みになってはいけないと、改めて認識させられる機会になりました。
出原さん その通りです。現場100日チャレンジに限らず、仕事を進める上では自分なりの仮説を立てて、アプローチをしていくことはとても大切だと思うのですが、それが先入観のように、強い思い込みになってはいけないと、改めて認識させられる機会になりました。
仕切り直しからの大発見 “お宝”データの活用に向けて
Arrow編集部 当初の想定と異なり、同じロットの中でも品質バラつきが平準化されていないことがわかったわけですが、出原さんの取り組みの方向性は変わりましたか?
出原さん はい。より細かい視点で「1ロット中のバラつきがわかるような情報は無いか?」というポイントに注目し、調査を続けました。事前の想定よりも確認するポイントが増えたため、負荷も増えましたが、その結果、非常に大きな発見をすることができました。天然ゴム1ロットを540個に細かくしたベールという単位があります。加工工場においては、9ベールに1つの割合で、測定している物性データがあることがわかったんです。これは私のようにゴム練り制御に取り組む人間にとっては、まさにお宝のようなデータです。先ほどお話した質問シートの改良は大変でしたが、結果的に有意義なヒアリングにつながり、このデータの存在を聞き出すことができました。また、これらのデジタルデータを、クラウドを介してタイヤ工場に接続することで、1ベールごとに適切な練り条件を適用して、練りゴム品質の均一化につなげられる可能性があります。
出原さん はい。より細かい視点で「1ロット中のバラつきがわかるような情報は無いか?」というポイントに注目し、調査を続けました。事前の想定よりも確認するポイントが増えたため、負荷も増えましたが、その結果、非常に大きな発見をすることができました。天然ゴム1ロットを540個に細かくしたベールという単位があります。加工工場においては、9ベールに1つの割合で、測定している物性データがあることがわかったんです。これは私のようにゴム練り制御に取り組む人間にとっては、まさにお宝のようなデータです。先ほどお話した質問シートの改良は大変でしたが、結果的に有意義なヒアリングにつながり、このデータの存在を聞き出すことができました。また、これらのデジタルデータを、クラウドを介してタイヤ工場に接続することで、1ベールごとに適切な練り条件を適用して、練りゴム品質の均一化につなげられる可能性があります。
自分も仲間も。みんなでチャレンジを続けていきたい
Arrow編集部 まさに天然ゴムとタイヤ製造をデジタルでつなぐ構想ですね!お話を聞いているだけでもわくわくしてきました。
出原さん もちろん、天然ゴムの加工工場で測定しているデータの他にも、加工後の経過日数や、輸送時の温湿度など、ゴムを練る直前まで物性に影響する要因は多くあります。今回発見した測定データのみを判断材料として、練り条件を決めることはできないので、実現に向けて残された課題をクリアするべく、私のチャレンジは続いていきます。ただ、今回の現場100日チャレンジに手を挙げなければ、気づくことが出来なかった事実であり、とても大きな進歩になったと思っています。
また改めて、今回の取り組みをサポートしてくれた、サプライチェーンのさまざまな関係者に御礼を申し上げたいです。私は昨年の10月から課長という立場になったのですが、当時の私のように、「チャレンジしたい!」と手を挙げてくれた仲間に対しては、マネジメントとして120%のサポートをして、背中を押してあげたいと思っています。
Arrow編集部 出原さんの今後の挑戦も応援しています!また、出原さんに続く、新しいチャレンジャーが続々と出てくるといいですね!
出原さん もちろん、天然ゴムの加工工場で測定しているデータの他にも、加工後の経過日数や、輸送時の温湿度など、ゴムを練る直前まで物性に影響する要因は多くあります。今回発見した測定データのみを判断材料として、練り条件を決めることはできないので、実現に向けて残された課題をクリアするべく、私のチャレンジは続いていきます。ただ、今回の現場100日チャレンジに手を挙げなければ、気づくことが出来なかった事実であり、とても大きな進歩になったと思っています。
また改めて、今回の取り組みをサポートしてくれた、サプライチェーンのさまざまな関係者に御礼を申し上げたいです。私は昨年の10月から課長という立場になったのですが、当時の私のように、「チャレンジしたい!」と手を挙げてくれた仲間に対しては、マネジメントとして120%のサポートをして、背中を押してあげたいと思っています。
Arrow編集部 出原さんの今後の挑戦も応援しています!また、出原さんに続く、新しいチャレンジャーが続々と出てくるといいですね!
ブリヂストンは創業時から、事業を通じて社会に貢献するために絶えず挑戦してきました。「挑戦」はまさにブリヂストンのDNAであり、自身はもちろん、誰かの挑戦を周りの仲間が後押しすることで、また新たなチャレンジが生まれます。そうして一人ひとりの成長と会社の成長が両輪となることで、変化に対応できるレジリアントな“エクセレント”ブリヂストンを実現できます。だからこそ、ブリヂストンはさまざまな施策を通じて、一人ひとりの挑戦をサポートしていきます。グループ報Arrowではそれぞれの立場・持ち場で挑戦を続ける仲間を紹介していきます!
【(株)ブリヂストン HRXカルチャーチェンジ・DE&I推進部より】
(株)ブリヂストンでは 2023年4月以降、計15名の開発企画職の皆さんが、海外含むさまざまな現場での100日チャレンジに取り組んでいます。新しいことへのチャレンジ、ハードルが高いと感じる方も多いと思いますが、普段から自分のやりたいこと、いっしょに働く仲間がやりたいと考えていることを職場内で共有し合い、色々な階層で現物現場での挑戦が生まれるようにしていくためにも、普段から、挑戦しようとしている仲間を後押しする気持ちを持つことが大切だと考えています。日々の業務において認識はしているものの、なかなか打破できないと感じている課題をお持ちの方も多くいらっしゃると思います。100日間、現場で集中して仮説の調査や検証を行い、それらを解決させたいという熱い想いをお持ちの方、ぜひ奮ってご応募ください!次回のプログラム募集開始は今年3-4月頃を予定しています!
(株)ブリヂストンでは 2023年4月以降、計15名の開発企画職の皆さんが、海外含むさまざまな現場での100日チャレンジに取り組んでいます。新しいことへのチャレンジ、ハードルが高いと感じる方も多いと思いますが、普段から自分のやりたいこと、いっしょに働く仲間がやりたいと考えていることを職場内で共有し合い、色々な階層で現物現場での挑戦が生まれるようにしていくためにも、普段から、挑戦しようとしている仲間を後押しする気持ちを持つことが大切だと考えています。日々の業務において認識はしているものの、なかなか打破できないと感じている課題をお持ちの方も多くいらっしゃると思います。100日間、現場で集中して仮説の調査や検証を行い、それらを解決させたいという熱い想いをお持ちの方、ぜひ奮ってご応募ください!次回のプログラム募集開始は今年3-4月頃を予定しています!
※「コメントする」を押してもすぐにはコメントは反映されません。
管理者にて確認の上、反映されます。コメント掲載基準については こちら をご覧ください。
尚、投稿者につきましては、管理者でも特定できない仕様になっております。