「BCMA」によるビジネスコストダウン効果創出推進モデル工場・栃木での取り組み
「BCMA」展開率「80%」達成を目指して
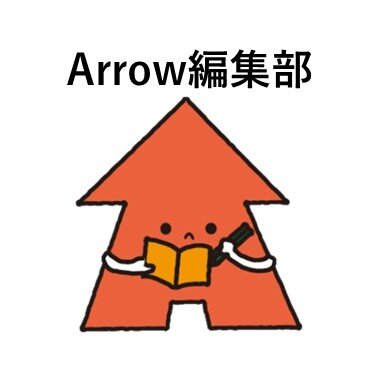
「BCMA」導入の経緯とこれまでの成果を教えてください。
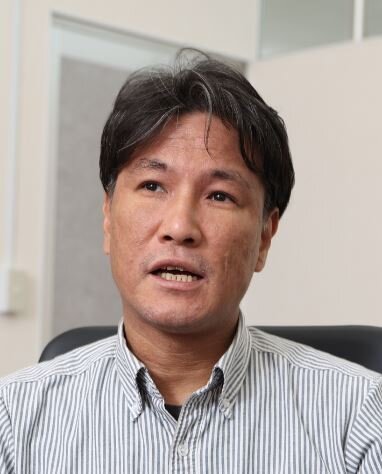
栃木がモデル工場に選ばれた理由は、まず日本のモノづくり拠点であることです。そして、「BCMA」は乗用車用タイヤとトラック・バス用タイヤの両方に導入されていますが、それら両方を生産する工場であること、また関東近辺の需要地に商品を供給するロケーションに恵まれ、物流費の効率化の効果が出やすいこと、更には「BCMA」の概念を踏まえて設計されたタイヤの生産比率(「BCMA」展開率)が国内で一番高かったことなどが挙げられます。現在30%程度の展開率を24MBPの期間で80%まで向上させることが私たちのミッションです。
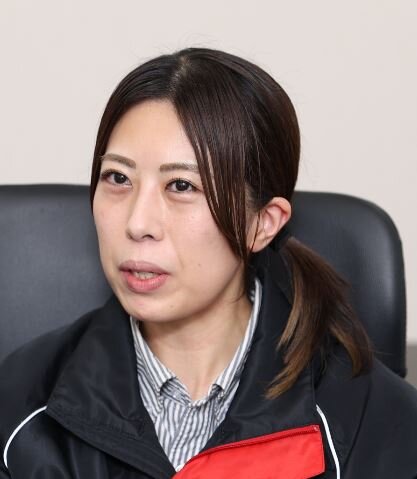
栃木工場では、1カ月で約150サイズを生産しています。また、タイヤの骨格部材であるビードやカーカスプライ等で構成されるケース、すなわちモジュール1については、1カ月で約140種類を製造しています。「BCMA」導入前は、販売計画に基づく生産切り替えが現場の負担になっていました。例えば、成型工程では、複数の材料を使います。巻物で送られてくる材料を台車ごと交換したり、材料自体を巻いている治工具を替えたりといった重労働が発生し、切り替えに1時間近くかかるものもあります。「BCMA」導入によりモジュール1のタイヤ骨格部の部材共用が進んできていることで、変更する材料の数が減ったり、試作件数が減ったりするなど、じわじわと効果が上がってきています。ただ、現場としてはまだその効果を体感しにくいことから、削減できたコストを定量化する取り組みを進めています。
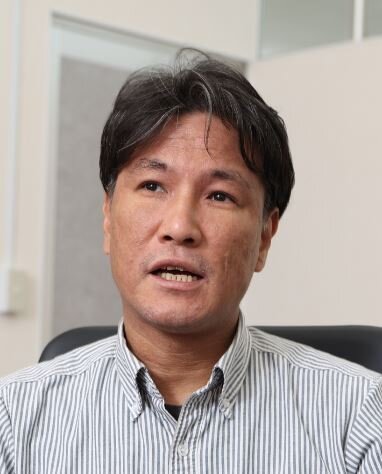
プレミアム化が進むとこれからもっと「薄く、軽く、円く」することを突き詰めることが必要になり、製造もより難しくなっていきます。「BCMA」によってモジュールの共用を進め、モノづくりをよりシンプルにしていく必要があること、それが、栃木工場でも長年追求してきた「スルラク生産」につながると考えています。モノづくりの方向性を理解し、「BCMA」を意識して、それぞれの現場で継続的な改善を進めていきたいですね。
工程能力を底上げし、 新しい改革 まだ見ぬ新しい価値の創出へ
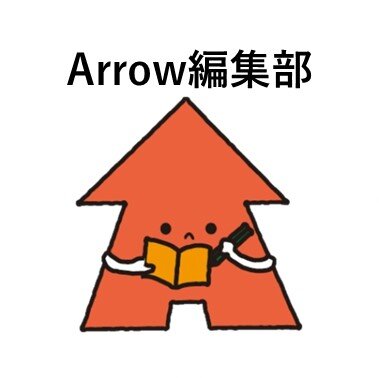
24MBPでの目標達成に向けた意気込みをお願いします。
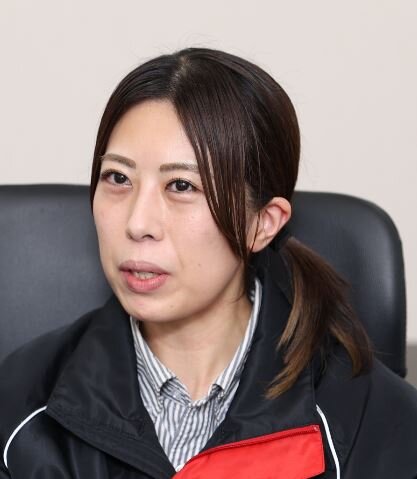
工場としての競争力を高めていくためにも、スルラク生産の実現に向けての改善に継続的に取り組んでいきます。「BCMA」や「ENLITEN」に対応した切り替え材料・切り替え回数の低減や、品質向上につながる工程能力の底上げを進めていきます。
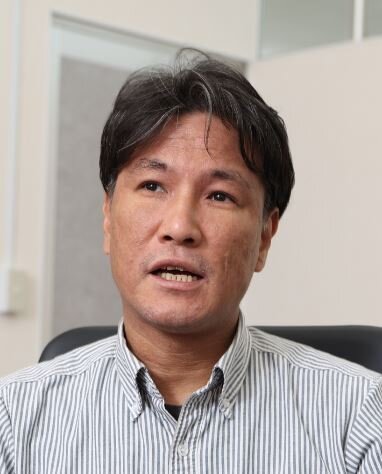
「BCMA」に則った量産体制を確立することと、工程能力の向上は、両輪で取り組んでいく必要があります。もし工程能力が十分でないままモジュールを共用すれば、同じモジュールを使う製品で一斉にトラブルが起こる事態にもなりかねません。工程能力を高める第一歩として、センシング機能などデジタルを活用しながら、工程能力を見える化し、改善につなげる活動も本年度から始めています。
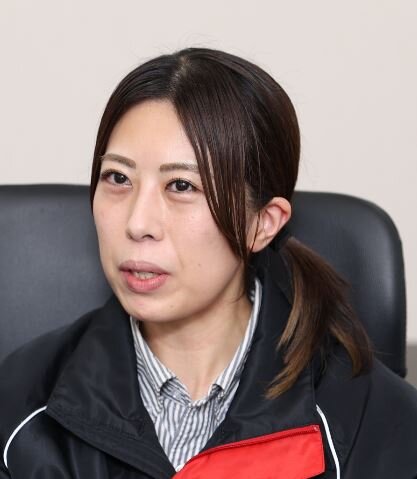
同じ成型機でモジュール共用されているものをバラつきなく連続生産することです。また、需要や販売計画、生産状況、出荷や物流のスケジュールなどいくつもの制約条件があるため、ロジックに落とし込んで最適な生産計画を組む必要があります。また、工程能力を高め、品質のバラつきをなくすことで生産性も上がり、省エネルギーなどグリーン化の実現もできるはずです。
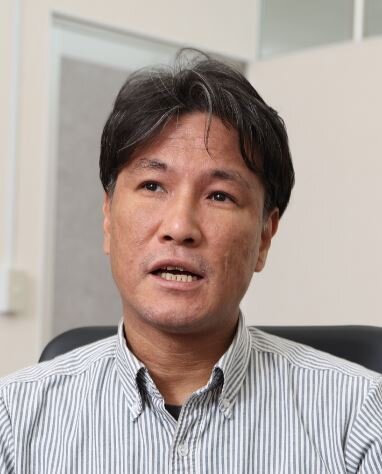
「BCMA」の導入で、工程能力の改善を進め、我々のモノづくりがどんな姿になっていくのか、どのような価値が生まれてくるのか、まだ見えてない部分が多くあります。スルラク生産の追求から、「品質へのこだわり」を実践し、新しい価値が次々と生まれていく、そんな流れを作っていければと思います。
※「コメントする」を押してもすぐにはコメントは反映されません。
管理者にて確認の上、反映されます。コメント掲載基準については こちら をご覧ください。
尚、投稿者につきましては、管理者でも特定できない仕様になっております。